What is the Maximum Slope for a Loading Dock?
Have you ever considered the importance of loading dock slopes in ensuring the safety and efficiency of your warehouse operations? A well-designed loading dock slope can drastically improve the ease of loading and unloading while reducing the risk of accidents and damage to equipment. In this blog post, we will delve into the world of loading dock slopes, exploring their significance, factors influencing their design, and the best practices to ensure optimal functionality and safety, including answering the question, “What is the maximum slope for a loading dock?”
As a business owner or warehouse manager, understanding loading dock slopes, and knowing what is the maximum slope for a loading dock, can be the key to maximizing productivity, reducing costs, and ensuring the well-being of your employees. So let’s dive into the world of loading dock slopes and discover how to make the most of this crucial aspect of your warehouse operations.
Short Summary
-
Understanding loading dock slope design is essential for warehouse and distribution center operations.
-
Adhere to OSHA regulations, industry best practices (1-2% grade), and consider factors such as truck bays, bay door size, safety features when designing a loading dock.
-
Implement forklift ramp safety tips & vehicle restraint systems to ensure safe usage of ramps & protect employees/equipment from potential risks.
Understanding Loading Dock Slopes
Loading dock slopes play a vital role in the daily operations of warehouses and distribution centers. They facilitate the smooth flow of goods between trucks and the loading platform, ensuring safety and optimizing efficiency, especially when it comes to loading dock doors. Several factors can affect enclosed loading dock design, such as:
-
Approaches that are not planned adequately
-
Doorways that are too small
-
Slopes that are too steep
-
Unsuitable bumper projections
The suggested inclination for a loading dock, considering the maximum grade capability, is approximately 1-2%.
A one-piece construction dock bumper is necessary for refrigerated doors to achieve a full seal around the dock and truck. Furthermore, portable dock plates should be used beneath the entrance for convenient insertion once the truck is properly docked, acting as a loading ramp. To ensure proper dock bumper projection, dock bumpers should be installed 1-2’’ below dock level, with sleeves anchors or lag bolts of recommended size used for flush loading dock design. Overlapping angles or a continuous bumper can help avoid trucks bumping into the wall in open loading dock design.
Factors Influencing Slope Design
When designing a loading dock slope, several factors must be considered, such as apron space, truck bays, and dock approach. The dock’s apron space, the area that precedes the bay door, is an important aspect of tooth loading dock design. To prevent depressions from forming during extreme heat, a concrete landing strip should be poured if asphalt is selected as the surface material for the apron space. The minimum displacement for truck bay doors, or dock doors, is generally 12’, with increased displacement facilitating simpler, safer, and more cost-effective loading processes, especially when proper dock bumper arrangements are in place.
Strategic forethought is necessary when implementing dock approaches that are declining or inclining, especially when considering loading dock doors. Additionally, materials required, traffic volume, and total length of vehicles received should all be factored in when evaluating the viability of an awning space. It’s crucial to make careful planning decisions when designing loading dock slopes to ensure the safety and efficiency of your loading dock operations.
Impact of Slope on Operations
The slope of a loading dock directly impacts the efficiency of loading and unloading, as well as the potential for accidents and damage to equipment. Here are some considerations:
-
Declining docks can bring the top portion of the trailer closer to the wall, potentially resulting in equipment and facility damage.
-
Inclined approaches present a similar issue due to the ICC bar getting closer to the facility wall below the bumpers.
-
If the decline or incline is too drastic, toppling may occur during loading/unloading, posing a significant risk to both employees and equipment.
To minimize these risks, it’s essential to carefully assess the slope of your loading dock and make necessary adjustments to ensure safe and efficient operations. By taking the time to understand the impact of slope on operations, you can make informed decisions that will serve to protect your employees, equipment, and overall productivity.
Maximum Slope Recommendations
To guarantee safe and efficient operations, maximum slope recommendations for loading docks are based on guidelines provided by the Occupational Safety and Health Administration (OSHA) and industry best practices. OSHA regulations stipulate that the maximum slope for a loading dock should not exceed a ratio of one vertical to three horizontal (20 degrees above the horizontal). By adhering to these slope guidelines, businesses can minimize risks and ensure employee safety.
In addition to OSHA guidelines, industry best practices recommend a grade of 1-2% for loading docks. Careful planning is required for declining or inclining docks to maintain efficiency and prevent potential hazards. By following these maximum slope recommendations when building ramps, warehouse managers and business owners can optimize their loading dock operations and create a safer working environment.
OSHA Guidelines
OSHA has established guidelines regarding loading dock slopes to reduce potential risks and ensure worker safety. The intent of these guidelines is to provide a safe working environment for employees and minimize the likelihood of accidents that could lead to injuries, damaged equipment, and costly downtime. As per OSHA regulations, the maximum slope for a loading dock should not exceed a ratio of one vertical to three horizontal (20 degrees above the horizontal).
By adhering to OSHA guidelines, businesses can prevent accidents and protect their employees while also reducing direct costs such as replacement labor, claims administration fees, lost production, and other process interruptions. Following OSHA guidelines for loading dock slope design is essential for maintaining a safe and efficient workplace.
Industry Best Practices
Industry best practices for loading dock slopes emphasize the importance of a 1-2% grade. This grade recommendation ensures efficient loading and unloading with manual pallet jacks and minimizes potential safety hazards. The American with Disabilities Act (ADA) Accessibility Guidelines also recommend a maximum slope of 1:12 for loading docks.
By following industry best practices and maintaining a 1-2% grade for loading docks, warehouse managers and business owners can optimize their loading dock operations, ensuring a smooth transition and safe working environment for their employees. Careful planning and adherence to these best practices can lead to reduced risks, increased efficiency, and ultimately, a more successful operation.
Loading Dock Design Considerations
When designing a loading dock, it’s crucial to take into account various factors such as dock and truck types trucks used, dock height, door size, and safety features to optimize functionality and safety. Different dock types, such as cantilever loading dock design, enclosed, flush, open, and saw tooth, can influence the slope of a loading dock and impact the ease of loading and unloading. Dock height and door size should be chosen to facilitate smooth product transfer and accommodate various truck types.
Implementing safety features such as dock bumpers, vehicle restraints, and forklift ramps can help prevent accidents and damage to equipment. By carefully considering all these factors, businesses can create a loading dock that maximizes efficiency, safety, and overall productivity.
Dock Types and Their Influence on Slope
Different dock types, such as:
-
Cantilever
-
Enclosed
-
Flush
-
Open
-
Saw tooth
Can influence the slope of a loading dock. Each dock type has its own unique characteristics and requirements, which can impact the overall design and functionality of a loading dock. For instance, enclosed loading docks may require additional considerations for ventilation and temperature control, while open loading docks may necessitate weather protection measures, such as an overhead canopy or canopies.
Understanding the various dock types and their influence on slope is essential for designing a loading dock that meets the specific needs of your business. By selecting the appropriate dock type and considering its impact on slope, you can ensure that your loading dock is both efficient and safe for your employees and equipment.
Dock Height and Door Size
The proper dock height and door size are essential factors to consider when designing a loading dock. The recommended dock height for a loading dock is usually between 48 and 52 inches. This height range allows for smooth product transfer and can accommodate various truck types, such as box trucks and tractor trailers.
When determining the appropriate height of a loading dock, it is essential to consider several factors to ensure a smooth product transfer. Some factors to consider include:
-
The height of the trucks or vehicles that will be loading and unloading at the dock
-
The height of the loading dock equipment, such as forklifts or pallet jacks that will be used
-
The height of the products being loaded or unloaded
Door size is another crucial consideration, as it determines the size of vehicles that can be accommodated at the loading dock. A well-designed loading dock should have doors that are large enough to facilitate efficient loading and unloading while also providing easy access for trucks and other vehicles.
By carefully considering dock height and door size, businesses can design a loading dock that maximizes efficiency and incorporates dock safety practices.
Dock Bumpers and Safety Features
Dock bumpers and safety features play a critical role in protecting loading docks from potential damage caused by trucks and trailers. Bumpers come in heights of 6-12 inches and can be stacked to achieve heights of 20-36 inches. A combination of horizontal and vertical bumpers can offer considerable protection for tractor trailers and the facility.
Moreover, vehicle restraint systems can be utilized to help mitigate the risk of accidents and damage to equipment in loading docks. Implementing safety features such as dock bumpers and vehicle restraint systems can minimize the likelihood of accidents and damage to equipment, averting expensive repairs and downtime.
By incorporating these safety features into your loading dock design, you can create a safer working environment for your employees while also protecting your valuable equipment and facility.
Loading Dock Ramp Safety
The loading dock ramp safety is of paramount importance, as it requires following forklift ramp safety tips and implementing vehicle restraint systems to reduce potential risks. Properly designed loading dock ramps can prevent forklift accidents, injuries, and fatalities, as well as minimize the risk of damage to equipment and facilities. By paying close attention to dock ramp safety, businesses can ensure a safe and efficient work environment for their employees.
In addition to forklift ramp safety tips, it’s crucial to implement vehicle restraint systems to provide protection, help avert trailer creep and reduce the hazards associated with not taking into consideration braking distance on a forklift ramp. By focusing on the safety of loading dock ramps, businesses can minimize risks, protect their employees and equipment, and maintain a safe and efficient working environment.
Forklift Ramp Safety Tips
When using a forklift ramp, it is important to:
-
Select the appropriate size
-
Inspect it prior to use
-
Drive with caution
-
Not exceed any weight restrictions
As per OSHA regulations, the maximum slope for a forklift ramp is 1 vertical to 3 horizontal (20 degrees above the horizontal). When travelling with an empty lift down a ramp, forklift operators should proceed in reverse. The lift’s forks should be pointed downwards at all times for safety.
Adhering to weight limits is critical to ensure ramp stability and prevent accidents. By following these forklift ramp safety tips, businesses can minimize the risk of accidents, injuries, and damage to equipment, ensuring a safe and efficient working environment for their employees.
Vehicle Restraint Systems
Vehicle restraint systems can help mitigate trailer creep and other safety risks associated with dock leveler operations. These systems can be classified into two primary categories: mechanical and hydraulic. Mechanical systems utilize a series of chains, cables, and other components to attach the trailer to the dock, while hydraulic systems employ a hydraulic cylinder to secure the trailer.
The utilization of vehicle restraint systems can provide several benefits, including:
-
Minimizing the likelihood of trailer creep, which can potentially cause accidents and injuries
-
Decreasing the amount of time required to secure a trailer to the dock
-
Lessening the amount of wear and tear on the dock itself
Implementing vehicle restraint systems is essential for the traffic flow and maintaining a safe and efficient loading dock environment.
Choosing the Right Dock Leveler Equipment
Selecting the right dock leveler can greatly enhance the efficiency and safety of your loading dock operations. Various equipment options include:
-
Dock levelers
-
Dock Plates
-
Edge-of-dock (EOD) levelers
-
Push button-operated dock levelers
When selecting a dock leveler, factors such as load capacity, width, galvanizing, type, and optional features should be taken into consideration. One of which is ease of installation. The EOD leveler can attach directly to the building wall or dock face. This greatly reduces installation costs.
By choosing the right dock leveler and taking into account factors such as:
-
length
-
width
-
lip projection
-
load capacity
-
activation system
Businesses can create a loading dock that is both efficient and safe for their employees and equipment. By investing in the proper equipment, warehouse managers and business owners can optimize their loading dock operations and ensure a safer, more productive work environment.
Dock Levelers and Plates
When selecting dock levelers and plates, one should take into account factors such as:
-
Length
-
Width
-
Lip projection
-
Load capacity
-
Activation system
The standard lip projection is 16 inches, with the minimum lip projection for a dock leveler required to be at least 4 inches as specified by ANSI MH30.1. Certain special rear step and rear door configurations on some trailers must be taken into account when determining the need for a longer lip projection for a dock leveler.
By carefully considering these factors and selecting the appropriate dock levelers and plates, businesses can optimize their loading dock operations and create a safer working environment for their employees. A well-designed loading dock with proper dock levelers and plates can greatly enhance the efficiency and safety of your warehouse operations.
Environmental Adaptations
Environmental adaptations, such as weather seals and insulation, can be utilized to maintain temperature control and protect equipment from corrosion. These adaptations can assist in safeguarding equipment from corrosion and sustaining temperature control, thereby enhancing the efficacy and safety of loading dock operations. When selecting the appropriate environmental adaptations, one should consider the climate, type of material handling equipment used and size of the loading dock.
By implementing these environmental adaptations, businesses can create a loading dock that is better suited to withstand the elements and provide a safer, more efficient working environment for their employees. As a result, businesses can reduce the risk of equipment damage, maintain temperature control, and ultimately improve the overall productivity of their loading dock operations.
Summary
In conclusion, understanding and designing the right loading dock slopes, adhering to OSHA guidelines and industry best practices, and considering factors such as dock types, dock height, dock door size, and safety features are all crucial to optimizing the efficiency and safety of your loading dock operations. By following the recommendations and tips shared in this blog post, businesses can create a loading dock that maximizes productivity, ensures employee safety, and reduces the potential for accidents and equipment damage.
As a warehouse manager or business owner, investing time and effort into understanding loading dock slopes and implementing the proper equipment and safety features can make a significant difference in the success of your operations. By making well-informed decisions and adhering to best practices, you can create a loading dock that is both efficient and safe, contributing to the overall success of your business.
Frequently Asked Questions
What is the maximum ramp slope for a loading dock?
The maximum ramp slope for a loading dock should be no more than 10%, though for heavy loads, it should be limited to 3-5%. Anything steeper increases the risk of loads toppling inside the truck bed.
What are the OSHA requirements for loading docks?
OSHA requires safety barriers at any dock with a drop of four feet or more. Employers must use chains or bars to create a barrier, as per 29 CFR 1910.28(b)(1)(i).
It is important to check up on local requirements when implementing these OSHA guidelines.
What is the slope of a warehouse ramp?
The slope of a warehouse ramp should not exceed a ratio of 1:3 (20 degrees above the horizontal) for safe operation with a forklift.
What are some important factors to consider when designing loading dock slopes?
When designing loading dock slopes, it is important to consider apron space, truck bays, dock approach, dock height, dock door size, and safety features such as dock bumpers and vehicle restraint systems to ensure optimal operation.
These features should be taken into account to ensure that the loading dock is efficient and safe for all users. Properly designed loading docks can help reduce the risk of accidents and improve the overall efficiency of the operation.
What types of loading dock equipment are available?
Loading dock equipment includes dock levelers, plates, edge-of-dock levelers, and push button-operated dock levelers, providing various loading dock protection solutions for various applications.
Have you ever considered the importance of loading dock slopes in ensuring the safety and efficiency of your warehouse operations? A well-designed loading dock slope can drastically improve the ease of loading and unloading, while reducing the risk of accidents and damage to equipment. In this blog post, we will delve into the world of loading dock slopes, exploring their significance, factors influencing their design, and the best practices to ensure optimal functionality and safety, including answering the question, “What is the maximum slope for a loading dock?”
As a business owner or warehouse manager, understanding loading dock slopes, and knowing what is the maximum slope for a loading dock, can be the key to maximizing productivity, reducing costs, and ensuring the well-being of your employees. So let’s dive into the world of loading dock slopes and discover how to make the most of this crucial aspect of your warehouse operations.
Short Summary
-
Understanding loading dock slope design is essential for warehouse and distribution center operations.
-
Adhere to OSHA regulations, industry best practices (1-2% grade), and consider factors such as truck bays, door size, safety features when designing a loading dock.
-
Implement forklift ramp safety tips & vehicle restraint systems to ensure safe usage of ramps & protect employees/equipment from potential risks.
Understanding Loading Dock Slopes
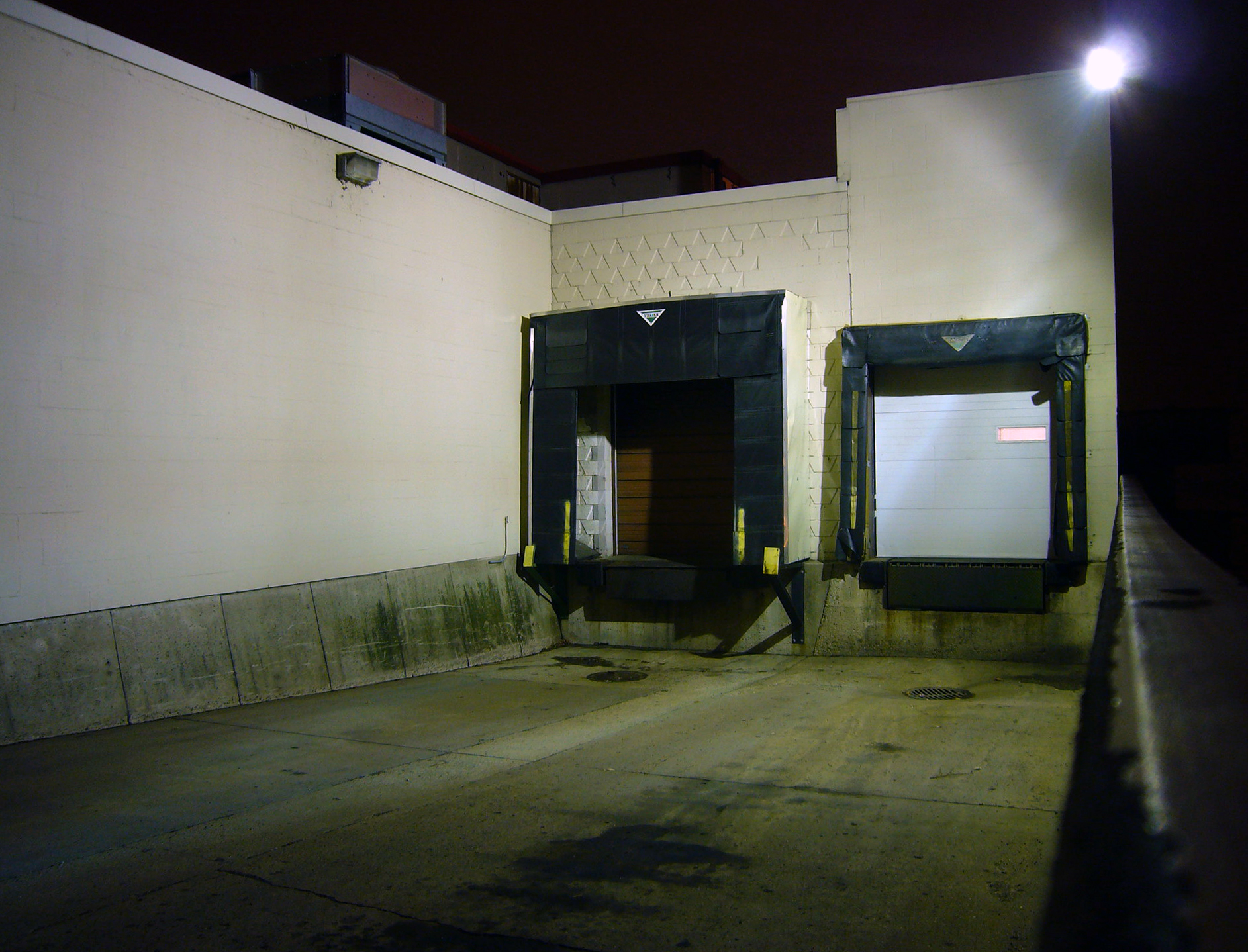
Loading dock slopes play a vital role in the daily operations of warehouses and distribution centers. They facilitate the smooth flow of goods between trucks and the loading platform, ensuring safety and optimizing efficiency, especially when it comes to loading dock doors. Several factors can affect enclosed loading dock design, such as:
-
Approaches that are not planned adequately
-
Doorways that are too small
-
Slopes that are too steep
-
Unsuitable bumper projections
The suggested inclination for a loading dock, considering the maximum grade capability, is approximately 1-2%.
A one-piece construction dock bumper is necessary for refrigerated doors to achieve a full seal around the dock and truck. Furthermore, portable dock plates should be used beneath the entrance for convenient insertion once the truck is properly docked, acting as a loading ramp. To ensure proper dock bumper projection, dock bumpers should be installed 1-2’’ below dock level, with sleeves anchors or lag bolts of recommended size used for flush loading dock design. Overlapping angles or a continuous bumper can help avoid trucks bumping into the wall in open loading dock design.
Factors Influencing Slope Design
When designing a loading dock slope, several factors must be considered, such as apron space, truck bays, and dock approach. The dock’s apron space, the area that precedes the bay door, is an important aspect of tooth loading dock design. To prevent depressions from forming during extreme heat, a concrete landing strip should be poured if asphalt is selected as the surface material for the apron space. The minimum displacement for truck bay doors, or dock doors, is generally 12’, with increased displacement facilitating simpler, safer, and more cost-effective loading processes, especially when proper dock bumper arrangements are in place.
Strategic forethought is necessary when implementing dock approaches that are declining or inclining, especially when considering loading dock doors. Additionally, materials required, traffic volume, and total length of vehicles received should all be factored in when evaluating the viability of an awning space. It’s crucial to make careful planning decisions when designing loading dock slopes to ensure the safety and efficiency of your loading dock operations.
Impact of Slope on Operations
The slope of a loading dock directly impacts the efficiency of loading and unloading, as well as the potential for accidents and damage to equipment. Here are some considerations:
-
Declining docks can bring the top portion of the trailer closer to the wall, potentially resulting in equipment and facility damage.
-
Inclined approaches present a similar issue due to the ICC bar getting closer to the facility wall below the bumpers.
-
If the decline or incline is too drastic, toppling may occur during loading/unloading, posing a significant risk to both employees and equipment.
To minimize these risks, it’s essential to carefully assess the slope of your loading dock and make necessary adjustments to ensure safe and efficient operations. By taking the time to understand the impact of slope on operations, you can make informed decisions that will serve to protect your employees, equipment, and overall productivity.
Maximum Slope Recommendations
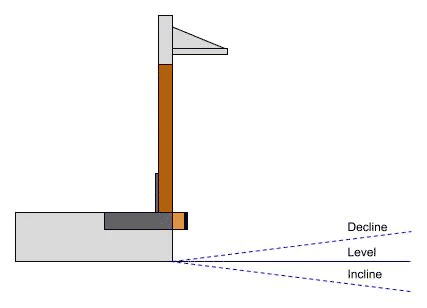
To guarantee safe and efficient operations, maximum slope recommendations for loading docks are based on guidelines provided by the Occupational Safety and Health Administration (OSHA) and industry best practices. OSHA regulations stipulate that the maximum slope for a loading dock should not exceed a ratio of one vertical to three horizontal (20 degrees above the horizontal). By adhering to these slope guidelines, businesses can minimize risks and ensure employee safety.
In addition to OSHA guidelines, industry best practices recommend a grade of 1-2% for loading docks. Careful planning is required for declining or inclining docks to maintain efficiency and prevent potential hazards. By following these maximum slope recommendations, warehouse managers and business owners can optimize their loading dock operations and create a safer working environment.
OSHA Guidelines
OSHA has established guidelines regarding loading dock slopes to reduce potential risks and ensure worker safety. The intent of these guidelines is to provide a safe working environment for employees and minimize the likelihood of accidents that could lead to injuries, damaged equipment, and costly downtime. As per OSHA regulations, the maximum slope for a loading dock should not exceed a ratio of one vertical to three horizontal (20 degrees above the horizontal).
By adhering to OSHA guidelines, businesses can prevent accidents and protect their employees while also reducing direct costs such as replacement labor, claims administration fees, lost production, and other process interruptions. Following OSHA guidelines for loading dock slope design is essential for maintaining a safe and efficient workplace.
Industry Best Practices
Industry best practices for loading dock slopes emphasize the importance of a 1-2% grade. This grade recommendation ensures efficient loading and unloading with manual pallet jacks and minimizes potential safety hazards. The American with Disabilities Act (ADA) Accessibility Guidelines also recommend a maximum slope of 1:12 for loading docks.
By following industry best practices and maintaining a 1-2% grade for loading docks, warehouse managers and business owners can optimize their loading dock operations, ensuring a smooth transition and safe working environment for their employees. Careful planning and adherence to these best practices can lead to reduced risks, increased efficiency, and ultimately, a more successful operation.
Loading Dock Design Considerations
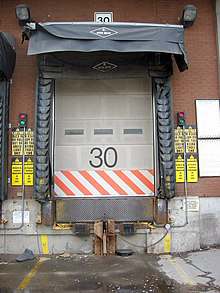
When designing a loading dock, it’s crucial to take into account various factors such as dock and truck types trucks used, dock height, door size, and safety features to optimize functionality and safety. Different dock types, such as cantilever loading dock design, enclosed, flush, open, and saw tooth, can influence the slope of a loading dock and impact the ease of loading and unloading. Dock height and door size should be chosen to facilitate smooth product transfer and accommodate various truck types.
Implementing safety features such as dock bumpers, vehicle restraints, and forklift ramps can help prevent accidents and damage to equipment. By carefully considering all these factors, businesses can create a loading dock that maximizes efficiency, safety, and overall productivity.
Dock Types and Their Influence on Slope
Different dock types, such as:
-
Cantilever
-
Enclosed
-
Flush
-
Open
-
Saw tooth
Can influence the slope of a loading dock. Each dock type has its own unique characteristics and requirements, which can impact the overall design and functionality of a loading dock. For instance, enclosed loading docks may require additional considerations for ventilation and temperature control, while open loading docks may necessitate weather protection measures, such as an overhead canopy or canopies.
Understanding the various dock types and their influence on slope is essential for designing a loading dock that meets the specific needs of your business. By selecting the appropriate dock type and considering its impact on slope, you can ensure that your loading dock is both efficient and safe for your employees and equipment.
Dock Height and Door Size
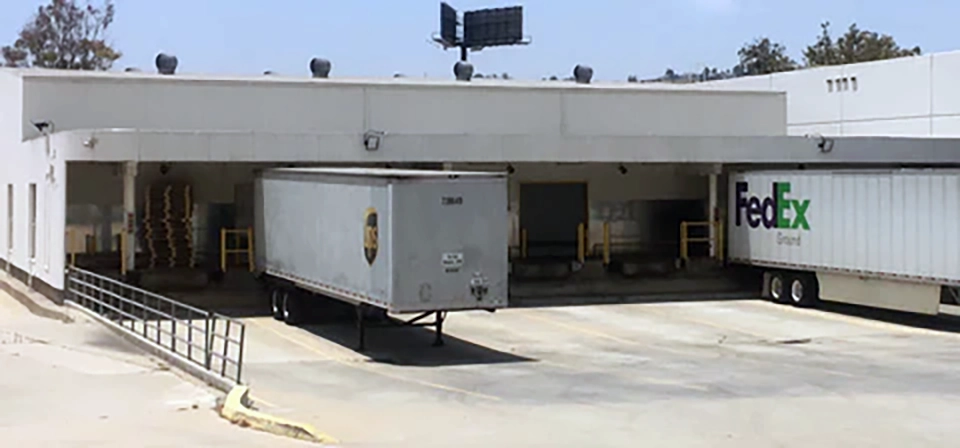
The proper dock height and door size are essential factors to consider when designing a loading dock. The recommended dock height for a loading dock is usually between 48 and 52 inches. This height range allows for smooth product transfer and can accommodate various truck types, such as box trucks and tractor trailers.
When determining the appropriate height of a loading dock, it is essential to consider several factors to ensure a smooth product transfer. Some factors to consider include:
-
The height of the trucks or vehicles that will be loading and unloading at the dock
-
The height of the loading dock equipment, such as forklifts or pallet jacks, that will be used
-
The height of the products being loaded or unloaded
Door size is another crucial consideration, as it determines the size of vehicles that can be accommodated at the loading dock. A well-designed loading dock should have doors that are large enough to facilitate efficient loading and unloading, while also providing easy access for trucks and other vehicles.
By carefully considering dock height and door size, businesses can design a loading dock that maximizes efficiency and incorporates dock safety practices.
Dock Bumpers and Safety Features
Dock bumpers and safety features play a critical role in protecting loading docks from potential damage caused by trucks and trailers. Bumpers come in heights of 6-12 inches and can be stacked to achieve heights of 20-36 inches. A combination of horizontal and vertical bumpers can offer considerable protection for tractor trailers and the facility.
Moreover, vehicle restraint systems can be utilized to help mitigate the risk of accidents and damage to equipment in loading docks. Implementing safety features such as dock bumpers and vehicle restraint systems can minimize the likelihood of accidents and damage to equipment, averting expensive repairs and downtime.
By incorporating these safety features into your loading dock design, you can create a safer working environment for your employees while also protecting your valuable equipment and facility.
Loading Dock Ramp Safety
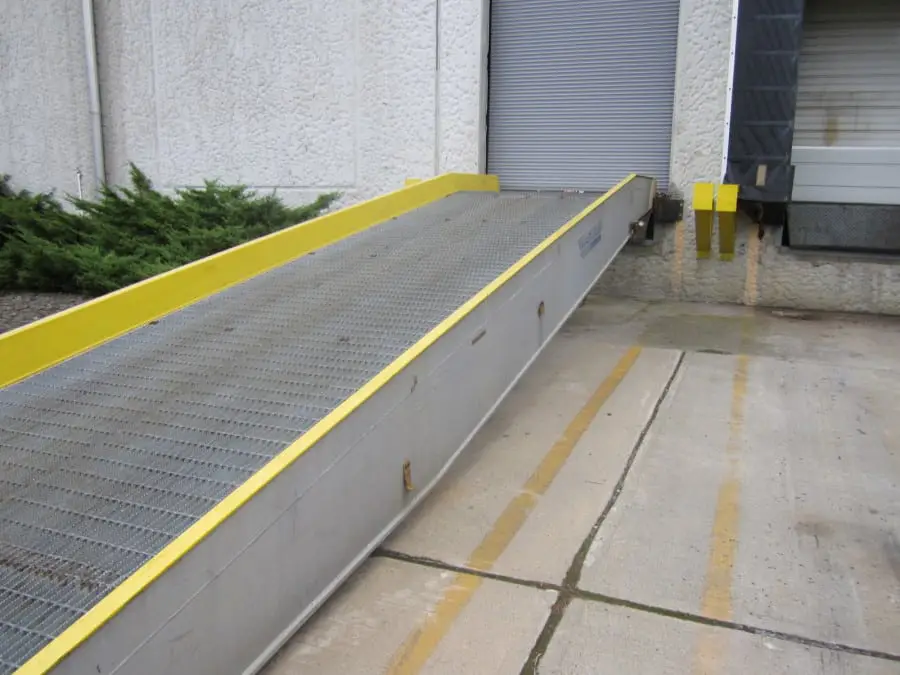
The loading dock ramp safety is of paramount importance, as it requires following forklift ramp safety tips and implementing vehicle restraint systems to reduce potential risks. Properly designed loading dock ramps can prevent forklift accidents, injuries, and fatalities, as well as minimize the risk of damage to equipment and facilities. By paying close attention to dock ramp safety, businesses can ensure a safe and efficient work environment for their employees.
In addition to forklift ramp safety tips, it’s crucial to implement vehicle restraint systems to provide protection, help avert trailer creep and reduce the hazards associated with not taking into consideration braking distance on a forklift ramp. By focusing on loading dock ramp safety, businesses can minimize risks, protect their employees and equipment, and maintain a safe and efficient working environment.
Forklift Ramp Safety Tips
When using a forklift ramp, it is important to:
-
Select the appropriate size
-
Inspect it prior to use
-
Drive with caution
-
Not exceed any weight restrictions
As per OSHA regulations, the maximum slope for a forklift ramp is 1 vertical to 3 horizontal (20 degrees above the horizontal). When travelling with an empty lift down a ramp, forklift operators should proceed in reverse. The lift’s forks should be pointed downwards at all times for safety.
Adhering to weight limits is critical to ensure ramp stability and prevent accidents. By following these forklift ramp safety tips, businesses can minimize the risk of accidents, injuries, and damage to equipment, ensuring a safe and efficient working environment for their employees.
Vehicle Restraint Systems
Vehicle restraint systems can help mitigate trailer creep and other safety risks associated with loading dock operations. These systems can be classified into two primary categories: mechanical and hydraulic. Mechanical systems utilize a series of chains, cables, and other components to attach the trailer to the dock, while hydraulic systems employ a hydraulic cylinder to secure the trailer.
The utilization of vehicle restraint systems can provide several benefits, including:
-
Minimizing the likelihood of trailer creep, which can potentially cause accidents and injuries
-
Decreasing the amount of time required to secure a trailer to the dock
-
Lessening the amount of wear and tear on the dock itself
Implementing vehicle restraint systems is essential for the traffic flow and maintaining a safe and efficient loading dock environment.
Choosing the Right Loading Dock Equipment
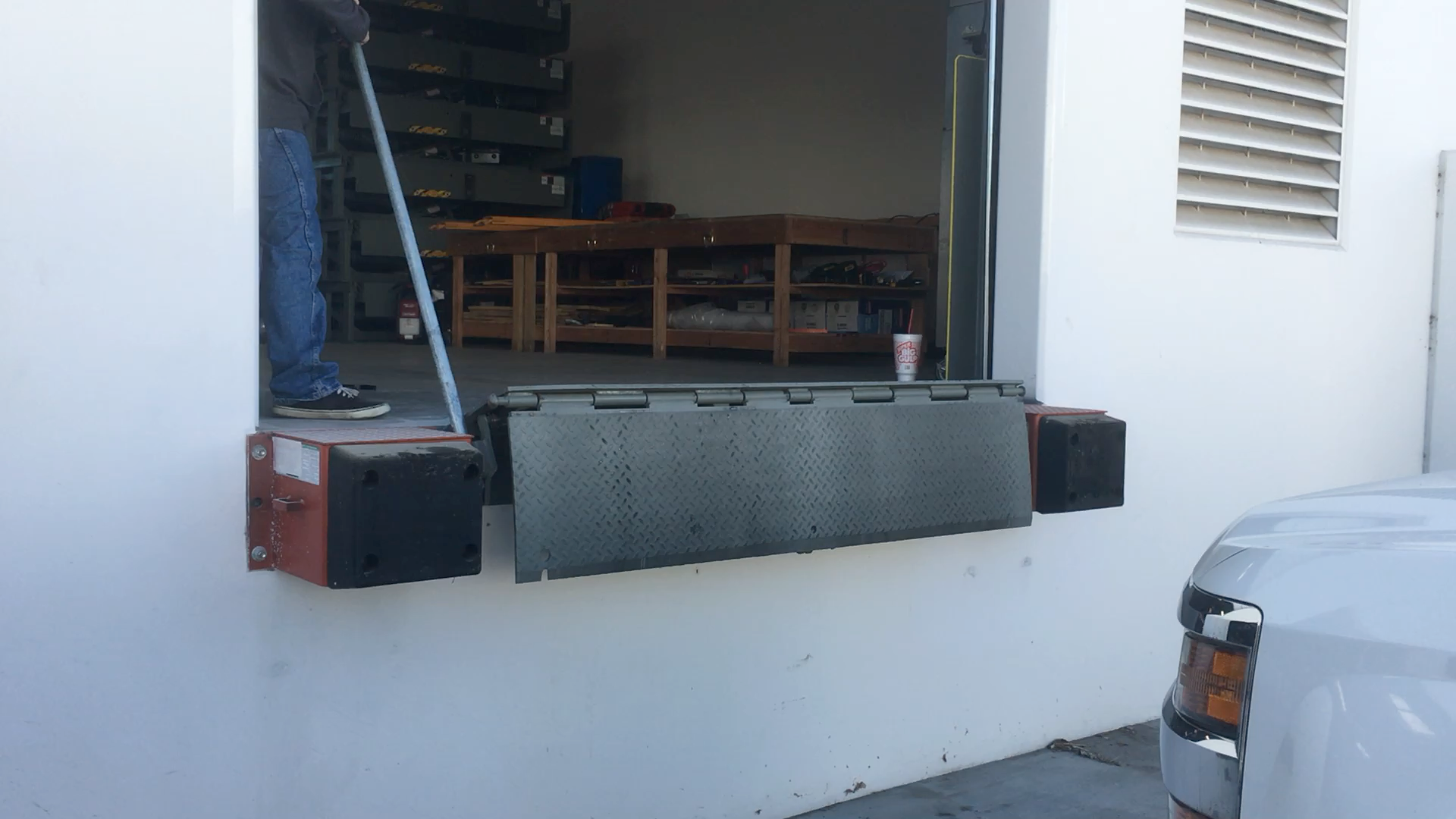
Selecting the right loading dock equipment can greatly enhance the efficiency and safety of your loading dock operations. Various equipment options include:
-
Dock levelers
-
Dock Plates
-
Edge-of-dock levelers
-
Push button-operated dock levelers
When selecting loading dock equipment, factors such as load capacity, width, galvanizing, type, and optional features should be taken into consideration.
By choosing the right loading dock equipment and taking into account factors such as:
-
length
-
width
-
lip projection
-
load capacity
-
activation system
Businesses can create a loading dock that is both efficient and safe for their employees and equipment. By investing in the proper equipment, warehouse managers and business owners can optimize their loading dock operations and ensure a safer, more productive work environment.
Dock Levelers and Plates
When selecting dock levelers and plates, one should take into account factors such as:
-
Length
-
Width
-
Lip projection
-
Load capacity
-
Activation system
The standard lip projection is 16 inches, with the minimum lip projection for a dock leveler required to be at least 4 inches as specified by ANSI MH30.1. Certain special rear step and rear door configurations on some trailers must be taken into account when determining the need for a longer lip projection for a dock leveler.
By carefully considering these factors and selecting the appropriate dock levelers and plates, businesses can optimize their loading dock operations and create a safer working environment for their employees. A well-designed loading dock with proper dock levelers and plates can greatly enhance the efficiency and safety of your warehouse operations.
Environmental Adaptations
Environmental adaptations, such as weather seals and insulation, can be utilized to maintain temperature control and protect equipment from corrosion. These adaptations can assist in safeguarding equipment from corrosion and sustaining temperature control, thereby enhancing the efficacy and safety of loading dock operations. When selecting the appropriate environmental adaptations, one should consider the climate, type of material handling equipment used, and size of the loading dock.
By implementing these environmental adaptations, businesses can create a loading dock that is better suited to withstand the elements and provide a safer, more efficient working environment for their employees. As a result, businesses can reduce the risk of equipment damage, maintain temperature control, and ultimately, improve the overall productivity of their loading dock operations.
Summary
In conclusion, understanding and designing the right loading dock slopes, adhering to OSHA guidelines and industry best practices, and considering factors such as dock types, dock height, door size, and safety features are all crucial to optimizing the efficiency and safety of your loading dock operations. By following the recommendations and tips shared in this blog post, businesses can create a loading dock that maximizes productivity, ensures employee safety, and reduces the potential for accidents and equipment damage.
As a warehouse manager or business owner, investing time and effort into understanding loading dock slopes and implementing the proper equipment and safety features can make a significant difference in the success of your operations. By making well-informed decisions and adhering to best practices, you can create a loading dock that is both efficient and safe, contributing to the overall success of your business.
Frequently Asked Questions
What is the maximum slope for loading dock?
The maximum slope for a loading dock should be no more than 10%, though for heavy loads it should be limited to 3-5%. Anything steeper increases the risk of loads toppling inside the truck bed.
What are the OSHA requirements for loading docks?
OSHA requires safety barriers at any dock with a drop of four feet or more. Employers must use chains or bars to create a barrier, as per 29 CFR 1910.28(b)(1)(i).
It is important to check up on local requirements when implementing these OSHA guidelines.
What is the slope of a warehouse ramp?
The slope of a warehouse ramp should not exceed a ratio of 1:3 (20 degrees above the horizontal) for safe operation with a forklift.
What are some important factors to consider when designing loading dock slopes?
When designing loading dock slopes, it is important to consider apron space, truck bays, dock approach, dock height, door size, and safety features such as dock bumpers and vehicle restraint systems to ensure optimal operation.
These features should be taken into account to ensure that the loading dock is efficient and safe for all users. Properly designed loading docks can help reduce the risk of accidents and improve the overall efficiency of the operation.
What types of loading dock equipment are available?
Loading dock equipment includes dock levelers, plates, edge-of-dock levelers, and push button-operated dock levelers, providing a range of loading dock protection solutions for various applications.
really, I liked your all-valuable information and thank you for it in this time.
Owner, Parts Brite
My background is in Electrical and Software Engineering, but since I started PartsBrite.com in 2016, I've focused on everything related to docks.
My team and I are here to help those looking to repair or replace their dock levelers, bumpers, door, and door lights.
1-855-PartsBrite | partsbrite.com | paul@partsbrite.com
Leave a comment